This is the fourth in a series of What to Look For in Your Next Warehouse Management System. Prior posts have covered how to decrease your warehouse associate onboarding time, the power of a well-designed WMS user experience, and key WMS features for subscription-based businesses.
The pack station. A mythical place, full of wonder and joy. A place of serenity and efficiency.
If only.
For most fulfillment centers, the pack station is, simply put, a mess.
It is here that associates are tasked with placing the products into the right box, utilizing the proper dunnage, inserting necessary receipts or other inserts, affixing the proper label, or assembling the branded kit. Any error could mean chaos - increased parcel fees, incorrect or broken products, or orders being sent to the wrong customer. And means a poor customer experience.
What’s worse, is a poorly planned pack station doesn’t just create the occasional errors…it creates a cascading runaway train of errors, leaving your team in a terrible predicament of compounding issues, with no Spider-Man to help slow things down.
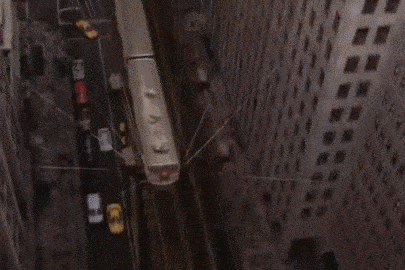
Today’s blog post, and associated video, explores the complexities of the pack station, and how a modern warehouse management system (WMS) can dramatically improve the efficiency for businesses, or 3PLs, managing high volume DTC fulfillment (without the need of a radioactive spider-bitten teenager).
Your Warehouse’s Last Line of Defense
This seems obvious. It is here where you can catch and correct any problems that occurred in the picking process. It is also here where the positive (or negative) customer experience is determined (e.g., unboxing experience) depending on the quality of the packing/kitting and parcel rate selection.
It is a lot of pressure, which means your WMS needs to set your team up for success. In fact, the right WMS can act a bit like spidey-sense.
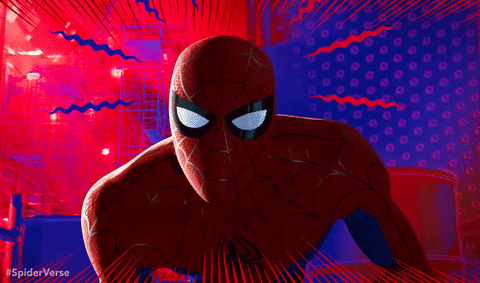
Imagine yourself at a pack station, a conveyor belt to your left, a computer in front of you, and surrounding you are endless boxes of differing sizes, mailers, inserts, and other odds and ends. A picked order comes down the belt, you scan the item(s) and… now what?
For some, these associates are left to quite literally “figure it out themselves” - they select whatever packaging they like and send it on its way. Don’t get caught in this web of inefficiency.
Instead, let’s explore how an efficient pack station operates differently.
That same picked order comes down the belt, you scan it, but now with a modern WMS implemented, the packaging type has already been configured and the computer immediately prompts you to select the properly sized box. By scanning that box, the system acknowledges the proper selection and prints the needed label and inserts.
If the product arrived at your station and is capable of being Shipped in Original Packaging (SIOP), upon scanning, the WMS would recognize this status, alert the associate to the proper next step (perhaps this is Nested Packaging allowing inclusion of other items within the original package), prints the label, and gets that order out the door.
Handling Warehouse Pack Station Exceptions
Pack stations clearly have a lot of responsibilities and must be flexible to handle different kinds of picking and packing setups (discrete, SLIPsteams, cluster, bulk, etc), or business models, like subscriptions, which you can read more about here.
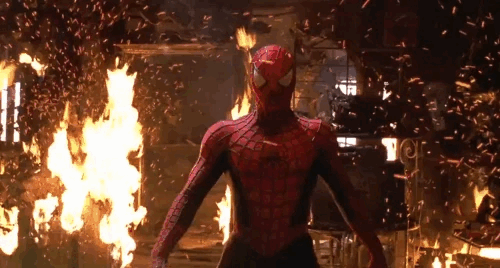
But this flexibility needs to extend beyond accommodating the ideal flow of orders and be equally capable of handling the exceptions.
Exception handling at the pack station is a crucial, and often overlooked, part of ensuring a smooth fulfillment.
Your modern WMS needs to be able to identify the exception error, which can occur for a few reasons:
Missing Product: when the expected product for packing is not in the tote
Wrong Product: when the product in the tote is different from the desired product
Incomplete Address: rather straightforward, this address cannot be validated for the chosen service method
A truly great WMS goes further, and after exception identification, has a thoughtful handling process.
Often a “Do Not Ship” label will be printed to prevent the incorrect order from leaving the facility. In tandem, the label will trigger the creation of an exception tote and insert the reason for the exception. This then empowers the team to triage and resolve the issue.
This can be as simple as picking the correct product and performing an inventory adjustment, or (with automated workflows) automatically performing predetermined next steps like “shipping less than full” and sending the customer automated updates regarding the changes made to her order.
With Great Power Comes Great Efficiency
Ok, THAT is the last Spider-Man reference, I promise, but Uncle Ben is right.
With all this great power a modern WMS can provide at the pack station does come great efficiency.
But in order to truly master this power, your associates don’t need cool spandex super-suits or even superpowers…they need an intuitive user interface (well, that is a WMS superpower!).
Having all of these amazing tools and capabilities is only as useful as it is easy-to-use.
If your exception handling is convoluted and labor intensive, you will experience increased slowdowns at your pack station. If your WMS does not give clear step-by-step packing instructions, you will inevitably ship things incorrectly, usually incurring more parcel expense and harming your customers’ experience.
Bringing Efficiency to Your Warehouse Operations
To truly have an efficient pack station, you must design for simplicity. When your team has thousands of orders to fulfill per day, even one additional click or scan within your WMS for each order will have a massive negative impact on productivity.
Every flow needs to be thoughtful with the intention of reducing actions, which is what we have built with Stord One Warehouse, our WMS that powers all of our fulfillment centers. You can read more about the need for ease-of-use within a WMS in this blog post.
Interested in getting your own WMS superpowers at your pack station? Let’s talk today about how Stord’s WMS can turn your team into superheros!
Pack Station Efficiency Video Recap
Having the right WMS is crucial to any operation.
The Pack station is the last line in the fulfillment chain process within a warehouse. You've already done your inbounding. You put aways. You had a picker, go and pick the item, and now you're ready to pack it out, give it a label, put it on a pallet ready to leave your building.
They have pictures of the items to avoid packing errors - match your SKU with what your packing.
Puts everything right in front of the packer.
Step A,
Step B,
Step C.
So instead of seeing all of this information up front, we say, “what's the first step of the process?”
Making sure that you always have the most accurate up to date weights.
If you're shipping internationally, it has your tariff codes, all of your customs information, make sure that you're getting the lowest packaging weight. It includes not just the weight for your product, but the wait for the corrugated.
Give you the best available shipping method.
From there, we make the choices in front of the packer very simple. The fastest shipping method and the correct package type.
It helps keep your inventory accuracy of your OPH up, keep you moving while maintaining accuracy within your system.
Still here? Ok, one more Spider-Man gif gift for you.
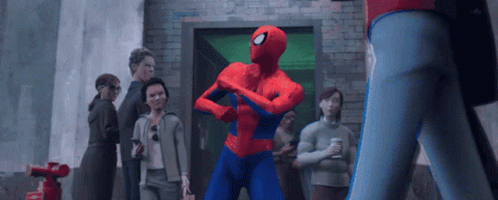